Category
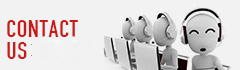
Contact person: Zhang Xingqian 13912340688
Phone: 0519-81182602
Fax: 0519-81182602
whatsapp:+8618961131360
Website: ggpxlxt.cn
Email: yz@yzdryer.com steven@yzdryer.com
GFZL series dry rolling granulator
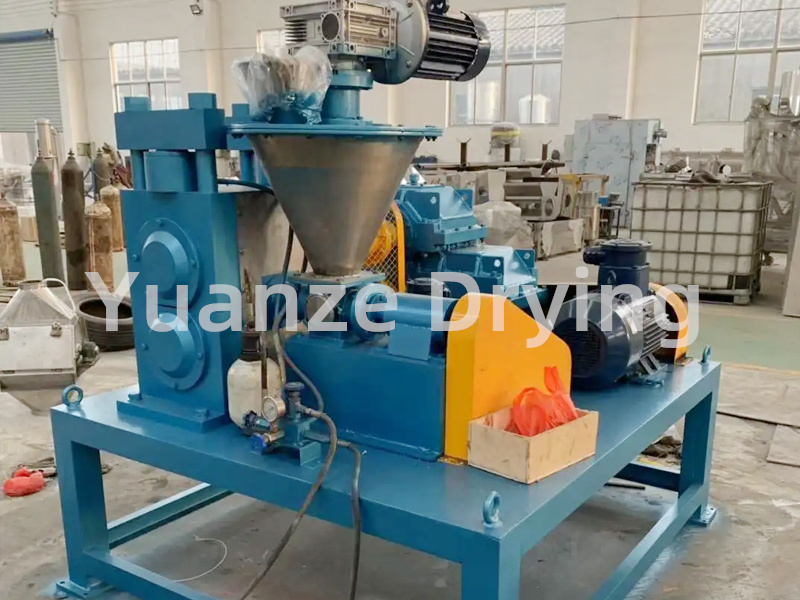


GFZL series dry rolling granulator
Description
Without any additives, dry powder can be directly granulated.
The particle strength can be adjusted by adjusting the pressure of the pressure roller to control the strength of the finished product.
Loop operation to achieve continuous production.
High finished product output, with a single machine output of over 2000kg/h (stacking density of 1.5) × 103kg/m3)
The powdered material is quantitatively fed by a vibrating feeder through a transverse spiral feeder, and uniformly fed into the main material hopper of the rolling mill to maintain a constant amount of material particles. Then, the powder is pre compressed by the longitudinal conical spiral inside the main material hopper of the rolling mill and transported to the arc-shaped grooves of the two pressure rollers. The surfaces of the two pressure rollers are evenly distributed with semi flat circular or diamond grooves of the same shape. Through the meshing transmission of a pair of gears, the two pressure rollers rotate at the same speed and in reverse, The material conveyed by the conical spiral to the groove is bitten into the groove and instantly forced to compress. After compression, the material gradually decreases with the pressure and falls off from the groove under its elasticity and gravity, entering the crushing and granulation system. Then, according to the user's particle size requirements, it is sieved and graded to obtain uniform granular products that meet quality requirements. The screened powder is then returned to the vibrating hopper for recycling.
Petrochemical, bioengineering, metal powder, fine chemicals, pharmaceuticals, food, pesticides, fertilizers, minerals, coal
Model/Project | GFZL-1 | GFZL-2 | GFZL-3 | GFZL-4 | GFZL-5 |
Roll diameter mm | φ240 | φ240 | φ300 | φ360 | φ480 |
Effective width of roller usage mm | 80 | 160 | 250 | 360 | 480 |
rpm | 8-20 | 8-20 | 8-20 | 8-20 | 8-20 |
t | 50 | 60 | 80 | 100 | 130 |
mm | 4 | 5 | 6 | 8 | 8 |
kg/h | 250-500 | 500-900 | 700-2000 | 1000-1400 | 2000-7400 |
mm | 0.2-5 | 0.2-5 | 0.2-8 | 0.2-8 | 0.2-8 |
kg/h | 80-150 | 150-300 | 300-600 | 600-1000 | 1000-2000 |
kw | 7.5 | 11 | 15 | 22 | 30 |
kw | 13 | 21 | 30 | 46 | 60 |
Long external dimensions × wide × high mm | 1500×2000×3800 | 1700×2000×4000 | 2000×2500×4200 | 2500×2500×5200 | 2800×2600×6000 |
weight t | 7 | 8 | 10 | 14 | 20 |
Note: 1. The rolling yield is calculated based on the material density of 1500kg/m3 and the rolling roller speed of 20rpm. 2. The finished product output is calculated based on 50% of the established quantity. 3. The particle size of the finished product can be adjusted over a large range by changing the sieve plate aperture of the crusher. 4. The actual power used by the host is 70% of the selected motor power. 5. The speed of the rolling mill is adjusted by changing the belt pulley transmission between the motor and the reducer. |