Category
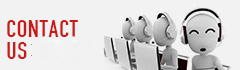
Contact person: Zhang Xingqian 13912340688
Phone: 0519-81182602
Fax: 0519-81182602
whatsapp:+8618961131360
Website: ggpxlxt.cn
Email: yz@yzdryer.com steven@yzdryer.com
LPG series high-speed centrifugal spray dryer
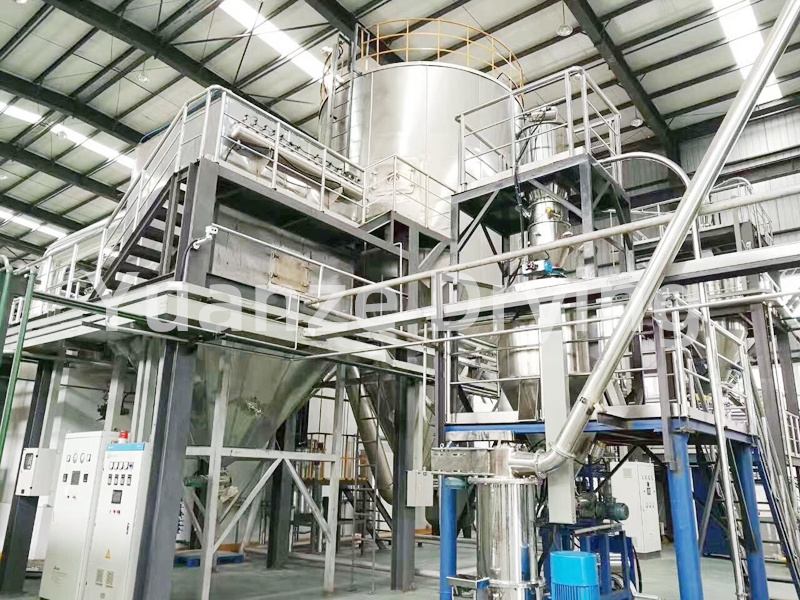


LPG series high-speed centrifugal spray dryer
Description
High speed centrifugal spray dryer is widely used in liquid forming process and drying industry. It is suitable for producing powder and granular solid products from suspended lotion, solution, lotion and paste liquid raw materials. Therefore, when the particle size distribution, residual moisture content, bulk density and particle shape of the finished product meet the precise standards, spray dryer is a very ideal drying process.
1. Spray drying speed is fast. After atomization, the surface area of the liquid material is greatly increased. In the process of contact with hot air, 95% -98% of the water can be evaporated instantly, and the drying time is only a few seconds. It is especially suitable for drying heat sensitive materials.
2. The product has good uniformity, fluidity, and solubility. The higher the purity of the product, the better the quality.
3. The production process of spray dryer is simplified, and the operation and control are convenient. For liquids with a moisture content of 40-60% (up to 90% for special materials), they can be dried into powder products in one go. After drying, there is no need for crushing and screening, reducing production processes and improving product purity. The particle size, bulk density, and moisture of the product can be adjusted within a certain range by changing the operating conditions, making control and management very convenient.
The spray dryer is open circulation, parallel flow and centrifugal atomization. The drying medium air is filtered by the primary and medium efficiency air filters, and then absorbed by the blower according to the operation instructions, heated by the heater, and enters the spray drying main tower through the hot air distributor of the high efficiency filter. The liquid material passes through the peristaltic pump according to the operating instructions and enters the high-speed rotating centrifugal nozzle. Under the action of centrifugal force, it is dispersed into small mist droplets. In the main spray drying tower, small droplets are in full contact with the hot air, and after heat exchange along their specific path, they are dried into products, which are then separated through the cyclone separator. Solid materials are collected, and the gas medium is filtered and discharged. The whole set of spray system is easy to clean and free of dead corners, meeting GMP requirements.
Chemical products: polyaluminum chloride, dispersed dyes, active dyes, organic catalysts, white carbon black, laundry detergent, zinc sulfate, silica, sodium metasilicate, potassium fluoride, calcium carbonate, potassium sulfate, inorganic catalysts, various waste liquids, etc.
Food: amino acids, vitamins, egg powder, bone meal, condiments, protein, milk powder, pig blood powder, soy sauce powder, coffee, tea, glucose, potassium sorbate, pectin, essence, spices, vegetable juice, yeast, starch, etc
Ceramics: alumina, zirconia, magnesium oxide, titanium oxide, magnesium titanate, clay, ceramic clay, various ferrite and metal oxides, etc
Key points:
1. Contact between hot air flow and fog drops: when enough hot air flow enters the spray drying chamber, the direction and angle of hot air flow must be considered, whether it is concurrent flow, countercurrent flow or mixed flow, to ensure full contact with fog drops, so as to carry out full heat exchange.
2. Atomization: The atomization system of the spray dryer must ensure the uniform distribution of the droplet size, which is crucial. Because this is the only way to ensure the qualification rate of product quality.
3. Design of pipe angle and cone angle: We have obtained some experience data from the production of nearly 1000 spray drying units, which can be shared with you.
Project/Parameters | LPG | |||||
5 | 25 | 50 | 100 | 150 | 200-2000 | |
Inlet temperature ℃ | 140~350 | |||||
Outlet temperature ℃ | ~80-90 | |||||
Water evaporation capacity kg/h | 5 | 25 | 50 | 100 | 150 | 200-2000 |
Rotating form of centrifugal spray head | Compressed air transmission | mechanical drive | ||||
speed(r.p.m) | 25000 | 18000 | 18000 | 18000 | 15000 | 8000-15000 |
Spray disc diameter (mm) | 50 | 100 | 120 | 140 | 150 | 180-340 |
heat source | electricity | Electricity+steam | Electricity+steam, fuel, gas | Solved by the user themselves | ||
Electric-heating power KW | 9 | 36 | 63 | 81 | 99 | |
Length×Width×Height (m) | 1.8×0.93×2.2 | 3×2.7×4.26 | 3.7×3.2×5.1 | 4.6×4.2×6 | 5.5×4.5×7 | Determine based on specific circumstances |
Dry powder recovery rate % | ≥95 | ≥95 | ≥95 | ≥95 | ≥95 | ≥95 |